Creating best practices by thinking outside the box
‘I love exploring new fields, and I enjoy working with people slightly more experienced than I am,’ says TMC Employeneur Jaap van der Heijden. ‘Colleagues who can teach me the fundamentals of their fields and then challenge me to come up with my own solutions.’ That’s precisely what happened during Jaap’s project at JACOBS DOUWE EGBERTS (JDE), The Netherlands’ iconic coffee company. Within a few months of entering a relatively new field, Jaap came up with a fresh approach to maintenance planning, hugely improving machine availability for production.
After having worked for ten years in a variety of roles – most of them on the IT-side of business pro-cesses – Jaap joined TMC Manufactering Support in June 2017. It took him less than a week to find the kind of project that truly excites him: working as a Maintenance & Reliability Engineer at JDE.
‘Originally, the idea was I’d work there for three months,’ Jaap says. ‘I was asked to plan and develop maintenance strategies for a new line of machines.’ In a few weeks, Jaap felt at home in his new role. JDE was satisfied as well, and asked him to stay on longer. It was a good decision: soon, Jaap and his team members came up with a completely new way of improving maintenance.
The Dedicated team
‘At JDE, I became a member of another, overarching team called the Dedicated team. The team brings together colleagues from various disciplines. Collectively, we looked for ways to consistently improve our department.’ One of the problems they looked at was with machine down-time. ‘We have two maintenance teams,’ Jaap explains. ‘autonomous maintenance and preventive maintenance. These teams used to work independently. Let’s say on Monday, team 1 works on a machine. The machine wouldn’t be in production during that time. Then, on Tuesday, team 2 does their rounds of inspections and maintenance work, which means another stop in production. It struck us that, in an ideal situation, maintenance would look like a Formula 1 pit-stop: we’d work with multiple teams at the same time on the same machine, thereby greatly reducing planned downtime for maintenance.’
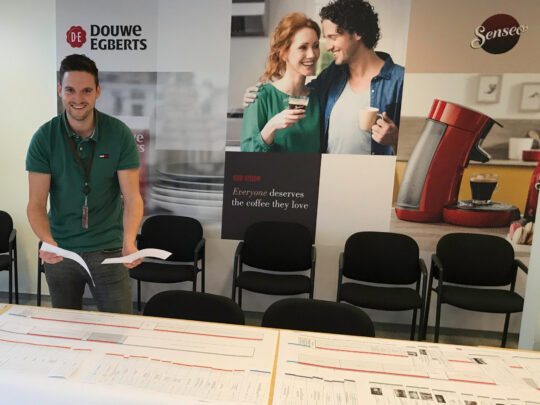
Piece of the puzzle
Jaap managed to bring the two maintenance teams together by translating their ideas into a huge puzzle, in which every maintenance task was represented by one piece. He mapped out and printed the timelines of both maintenance teams, specifying every step of the process and the exact amount of time, frequency and safety level these steps required. Next, he asked all the maintenance technicians to come together and put the pieces on the timelines in such a way that the tasks did not overlap - without compromising on safety or maintenance quality. ‘What made this approach successful was not just the puzzle approach itself,’ Jaap says, ‘it was the fact that the technicians actively solved the problem together and supported this new way of working in the organization. It became an exciting game.’
After a successful pilot period, Jaap presented his solution on JDE’s ‘best practice day’ to other senior managers and plant managers from several Western-European countries. The response was overwhelmingly positive.
Wonderful experience
‘It was a great way to end a wonderful experience,’ Jaap says. ‘At JDE, everybody’s part of one big team, and everyone I’ve worked with, in every kind of role, shows a strong commitment to the coffee roastery and its products. JDE offers its team members a lot of room for personal development - I’m living proof of that. This approach leads to remarkable results and a very pleasant, yet challenging atmosphere to work in.’
This month, Jaap starts at Bosch as Project Leader Maintenance. He’s looking forward to another new step – and the next challenge.